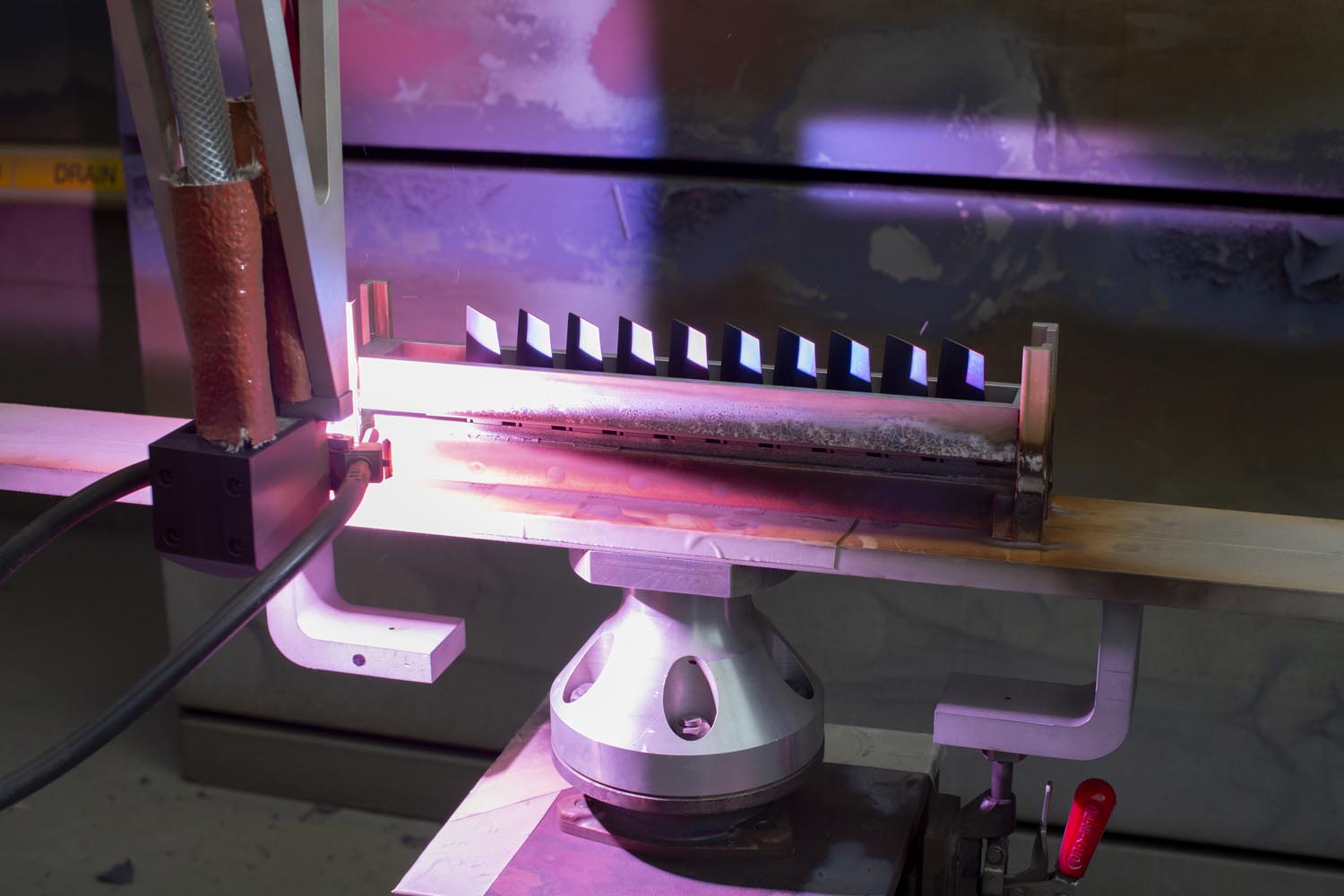
The leader in commercial & aerospace plasma and thermal-spray coatings
At Metallizing Service Company, we apply state-of-the-art and customized protective coatings for commercial, aerospace and industrial applications, with superior attention to customer specifications, accuracy and precise quality control. Every part or component coming into MSC has special handling, preparation and coating requirements. Our staff works closely with your service, engineering, quality and manufacturing personnel to ensure a partnership committed to coating excellence, on-time delivery and clear communication.
Our on-site services include:
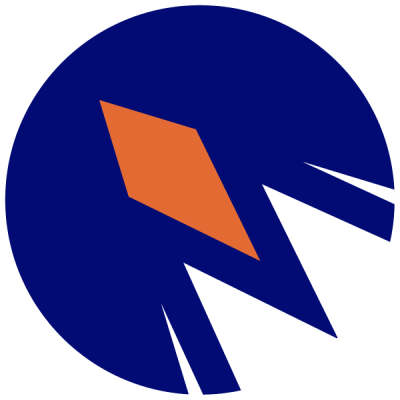
Laboratory facilities for metallurgical evaluation, quality assurance, and R&D of improved spraying applications and related technological research.
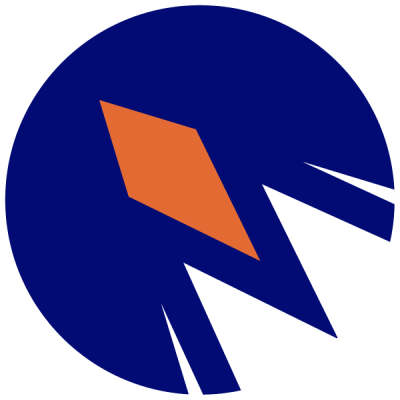
Machine shop pre-spraying preparation (grinding, undercutting) and finishing, as well as fabrication of fixtures for meeting your special coating challenges.
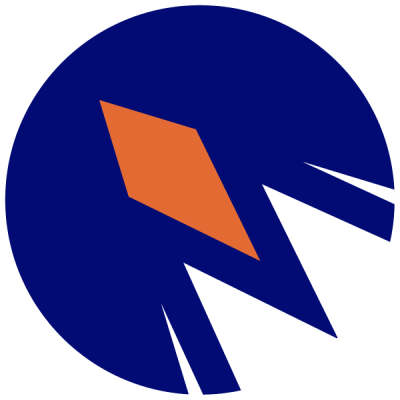
A large variety of grit blasting, thermal plasma and wire-spraying equipment, and a multitude of automation options.
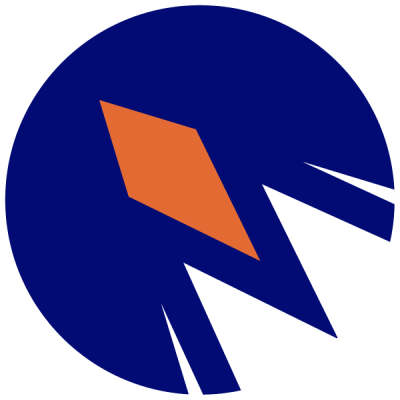
Robotic coating and other automated processes for intricate spraying challenges. We meet your technical requirements at a competitive cost.
Plasma Spray
Plasma spray is a high-temperature, high-energy coating process that utilizes a controlled plasma arc to heat and accelerate ceramic or metal powder feedstock onto a substrate. This process is extensively used in gas turbine engines for applying thermal barrier coatings (TBCs) on turbine blades, vanes, and combustor components, protecting them from extreme heat and oxidation.
Plasma spray is also widely used for abradable seal coatings in compressors and turbines, improving clearance control and enhancing overall engine efficiency. The ability to deposit dense, well-adhered coatings of materials such as yttria-stabilized zirconia (YSZ), aluminum oxide, and chromium carbide makes plasma spray a critical technology in aerospace and power generation. Beyond turbine applications, it is widely used for industrial wear coatings, providing surface enhancements for components exposed to high temperatures, abrasion, and mechanical stress.
Flame / Thermal Spray
Flame spray is a thermal spray process that utilizes a high-temperature combustion flame to melt and accelerate material—typically metal or ceramic powders—onto a substrate. While it does not achieve the same coating density and bond strength as more advanced spray processes, it remains a cost-effective method for applications that require moderate wear resistance, thermal protection, or dimensional restoration. In gas turbine engines, flame spray is commonly used for abradable coatings in clearance control systems, helping optimize efficiency by reducing unnecessary airflow leakage in compressors and turbines. In industrial applications, it serves as an economical repair process for worn parts such as pump sleeves, shafts, and general machinery components.
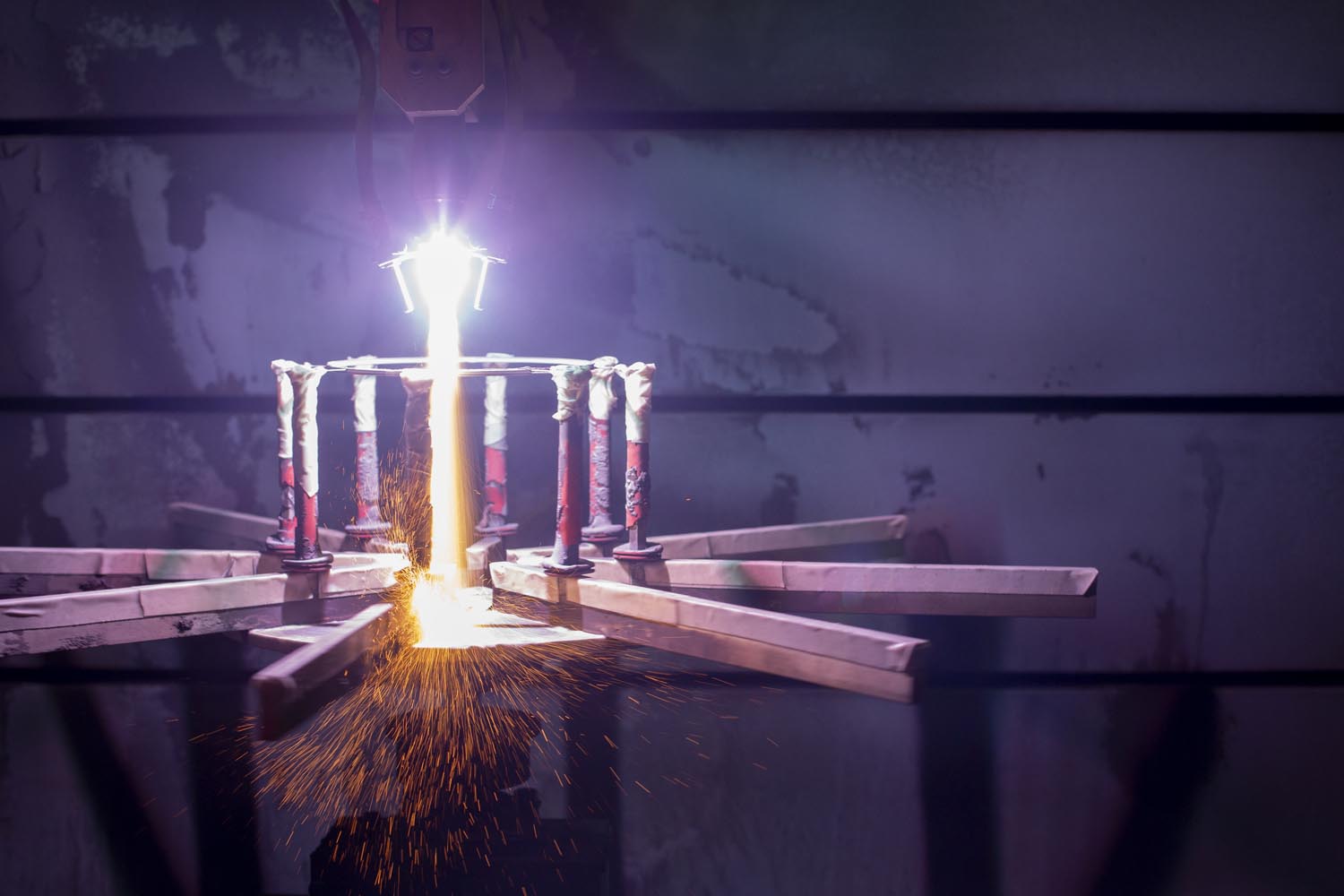
Wire Arc Spray
Wire arc spray operates by melting wire through an electric arc and atomizing the molten material with compressed air or inert gas to form a coating. This high-deposition process is particularly well-suited for dimensional restoration of worn components in gas turbines, industrial engines, and rotating machinery, such as bearing journals, shaft surfaces, and seal areas.
In turbine applications, wire arc spray is also used to apply abradable coatings for clearance control, particularly in compressor casings and shroud sections, where they help maintain optimal operating efficiency. These coatings provide robust wear resistance and improved performance for critical engine and mechanical components subjected to friction and high mechanical loads. It is frequently used in the repair and overhaul (MRO) sector to extend the service life of costly turbine parts and industrial equipment.
Interested in learning more?
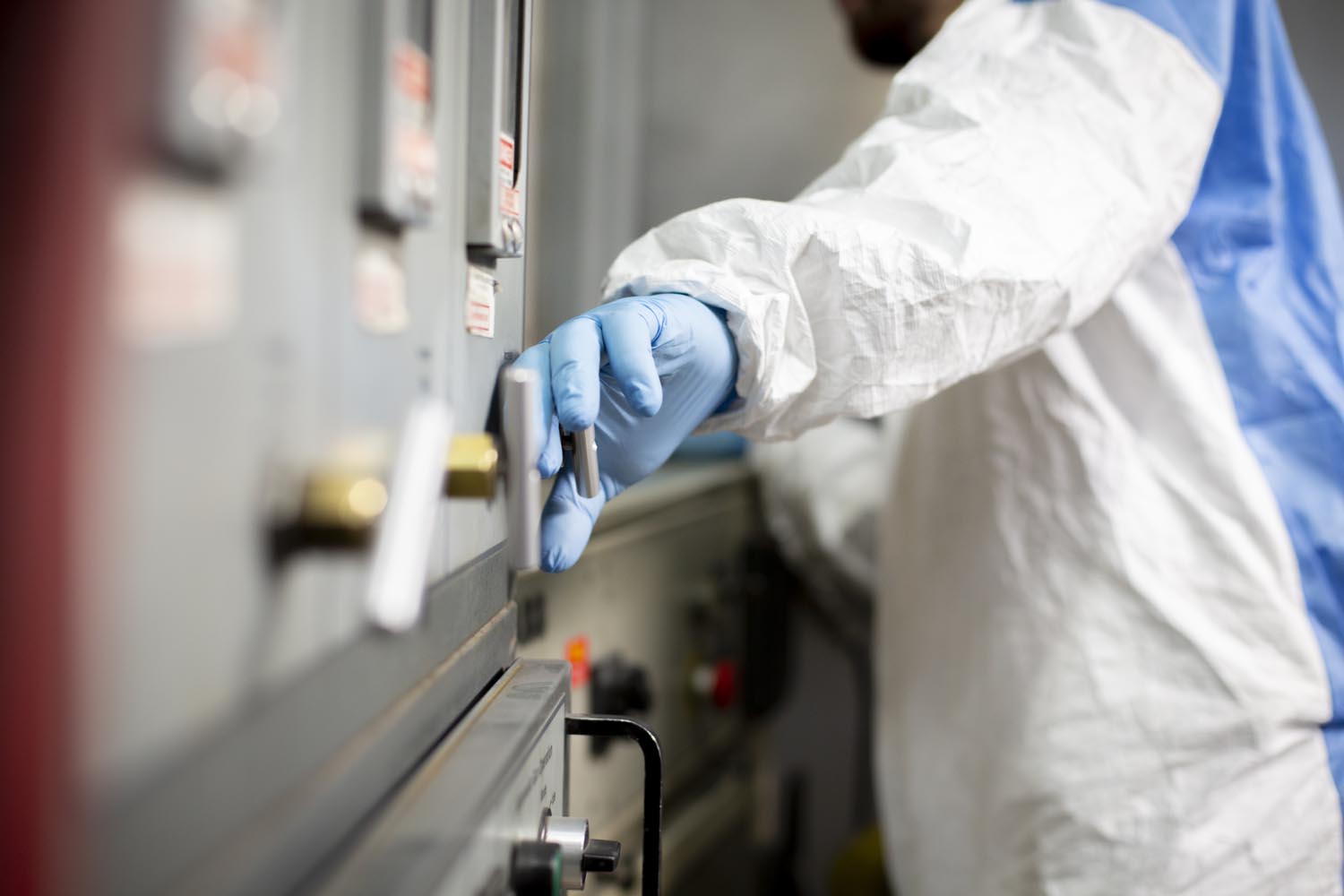
High-Energy Plasma Spray
High-energy plasma spray is an advanced plasma process designed for higher particle velocities and improved coating density, offering exceptional adhesion and durability in extreme environments. This technique is widely employed in gas turbine engines for thermal barrier coatings (TBCs), abrasive tip coatings, and oxidation-resistant layers on turbine blades, shrouds, and hot-section components.
This process enables the deposition of advanced ceramics such as YSZ, rare-earth oxides, and dense alumina coatings that can withstand high thermal loads. Industrial applications include high-wear coatings for pumps, extruder screws, and industrial rolls, where superior surface hardness and erosion resistance are required.
HVOF Spray
High-Velocity Oxygen Fuel Spray
HVOF spray is a high-energy thermal spray process that produces exceptionally dense, hard coatings with minimal porosity, making it a preferred choice for wear-resistant and erosion-resistant applications in gas turbines and industrial machinery. This process is commonly used to apply tungsten carbide, chromium carbide, and metallic alloys to compressor blades, turbine shafts, and bearing journals, significantly extending their operational life under extreme stress and particle erosion conditions.
HVOF is also used to apply abrasive coatings for clearance control systems, particularly in tip coatings on rotating components within turbines and compressors, ensuring precise operational clearances and improving efficiency. In addition to turbine engine applications, HVOF coatings are widely used in industrial power generation, oil and gas, and high-performance manufacturing, where components require superior hardness, fatigue resistance, and surface durability.
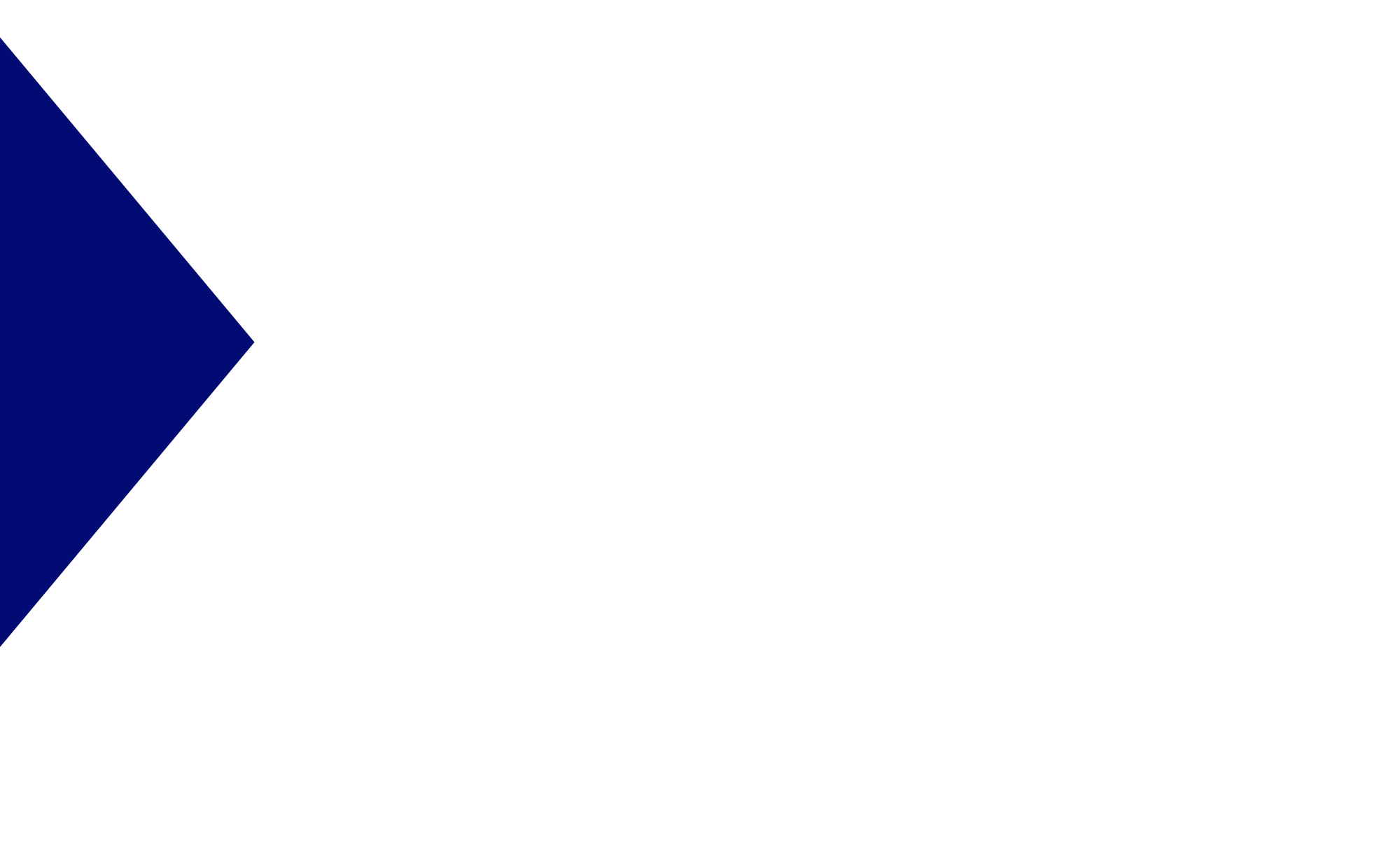
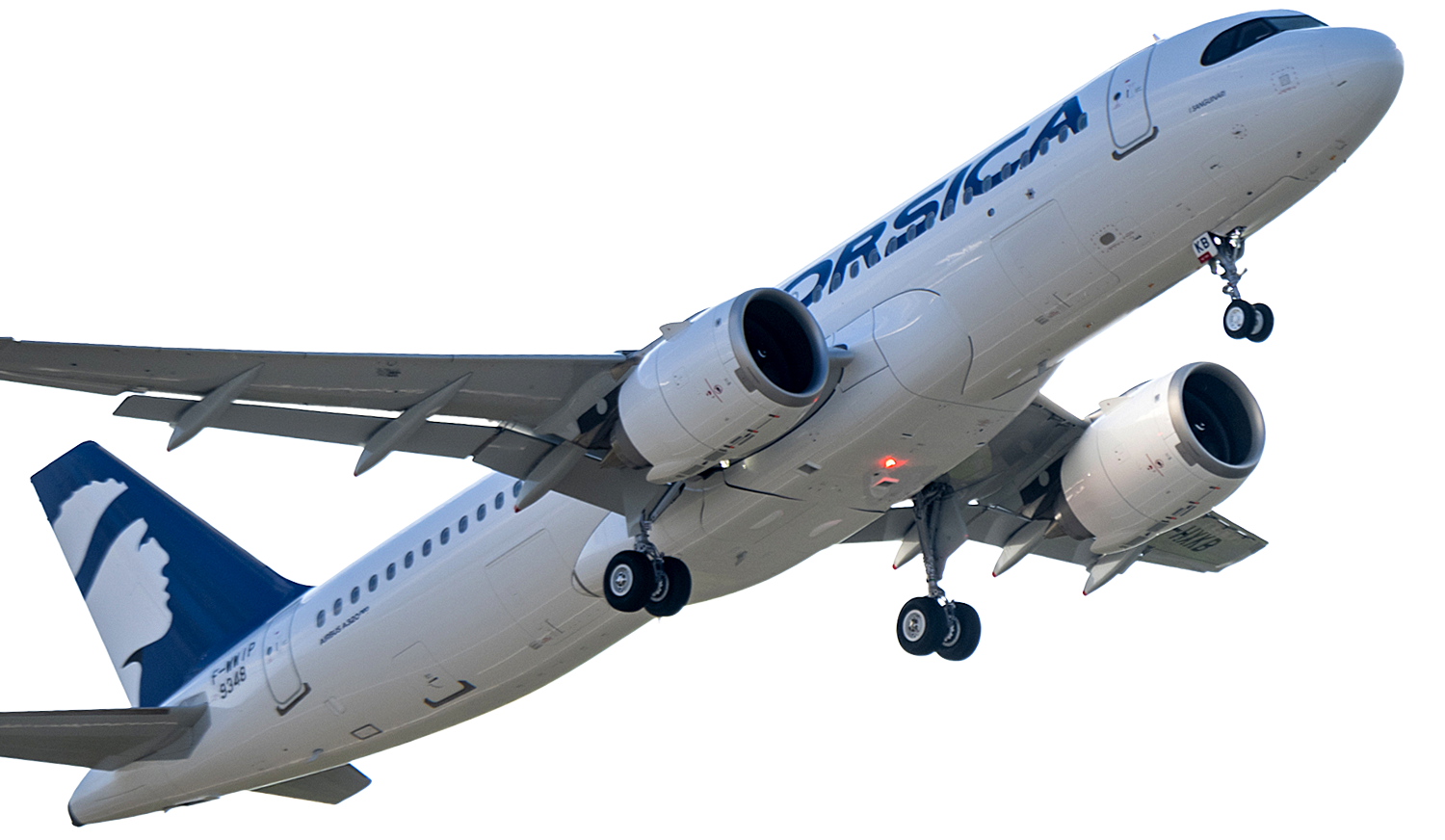